Factors That Affect CNC Machining Costs – and How to Reduce Them
2025.05.10
CNC machining is one of the most reliable methods for producing high-precision parts. It's widely used across industries such as aerospace, medical devices, electronics, and automotive manufacturing. However, due to the high capital investment in CNC machinery, most companies rely on specialized external partners for CNC production.
For product developers and engineers, minimizing part production costs while staying within budget is a constant challenge. In this article, we explore the key factors that influence CNC machining costs and outline practical strategies B2B companies can use to reduce expenses without compromising quality.
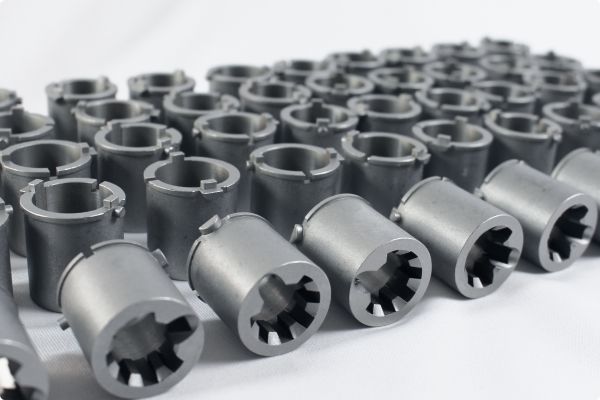
Key Factors That Influence CNC Machining Costs
1. Part Geometry and Size
The more complex or larger a part is, the longer it takes to machine—and the more raw material it requires. Complex geometries often demand multi-axis equipment (e.g., 3-axis, 5-axis) and additional setups, which significantly increase production time and cost.
2. Material Selection
CNC machining involves subtractive manufacturing—cutting away from a solid block of material. Therefore, material cost plays a major role in the overall price.
Aluminum is a popular choice due to its excellent machinability, lightweight properties, and cost efficiency. In contrast, high-strength alloys like titanium or Inconel are more difficult to machine, cause faster tool wear, and require specialized tools and equipment, driving costs up significantly.
3. Production Volume
CNC machining involves time-intensive setup tasks such as tool programming and calibration. For small production runs, this means a higher per-unit cost. However, the cost per part decreases significantly with volume. Where possible, consider batch production to improve cost-efficiency.
"By optimizing your design, you can minimize unnecessary complexity and significantly reduce time and production cost."
Proven Strategies to Reduce CNC Machining Costs
One of the most effective ways to reduce CNC machining costs is to apply Design for Manufacturability (DFM) principles early in the design process. By optimizing your design for ease of manufacturing, you can minimize unnecessary complexity and significantly reduce time and cost. Here’s how:
Avoid Thin Walls
Thin-walled parts are prone to deformation during machining, which lowers precision and quality—often leading to scrap or rework. As a rule of thumb, design metal parts with wall thicknesses of at least 0.8 mm, and plastic parts with 1.5 mm or more. If thinner sections are required, consider switching to sheet metal fabrication instead.
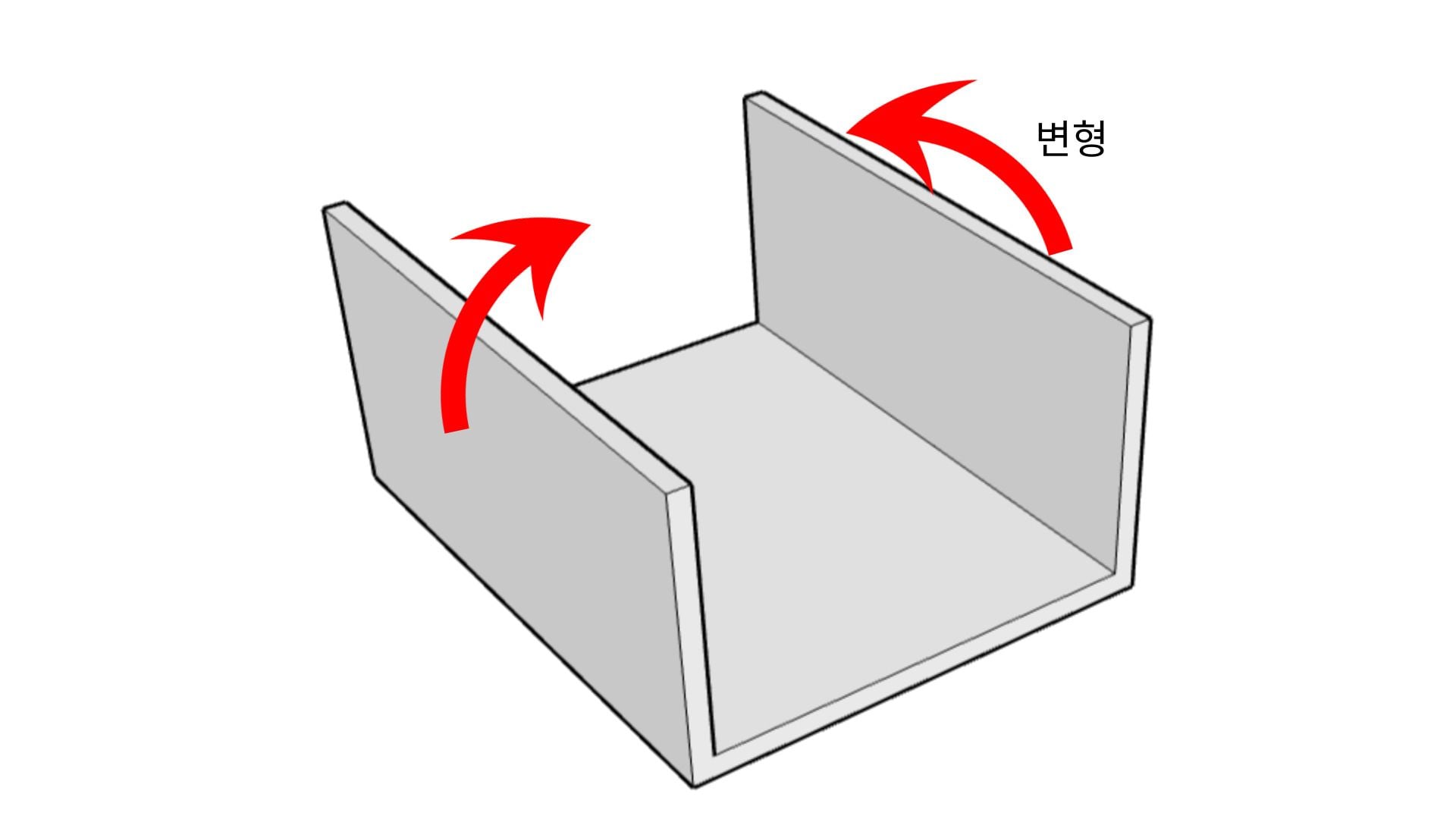
Limit Excessive Internal Depths
Deep internal cavities often require long, narrow tools, which are more prone to vibration, wear, and breakage. This not only increases machining time but may also reduce surface finish quality. Design internal features with optimal tool accessibility in mind.
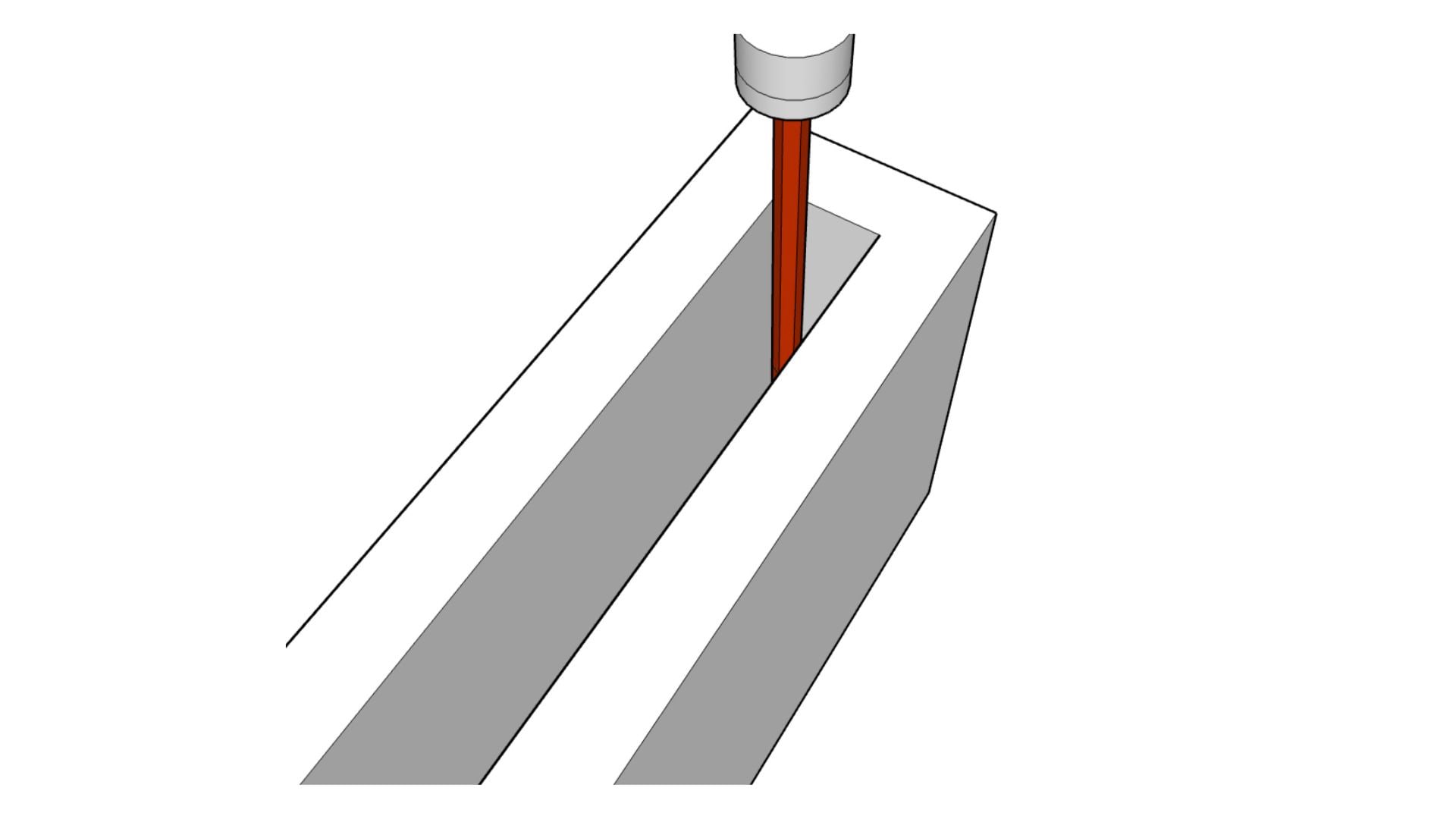
Consider Splitting Complex Parts
If a part has highly intricate features, it may be more cost-effective to modularize the design—machining simpler components separately and assembling them afterward. This reduces machining complexity and setup time.
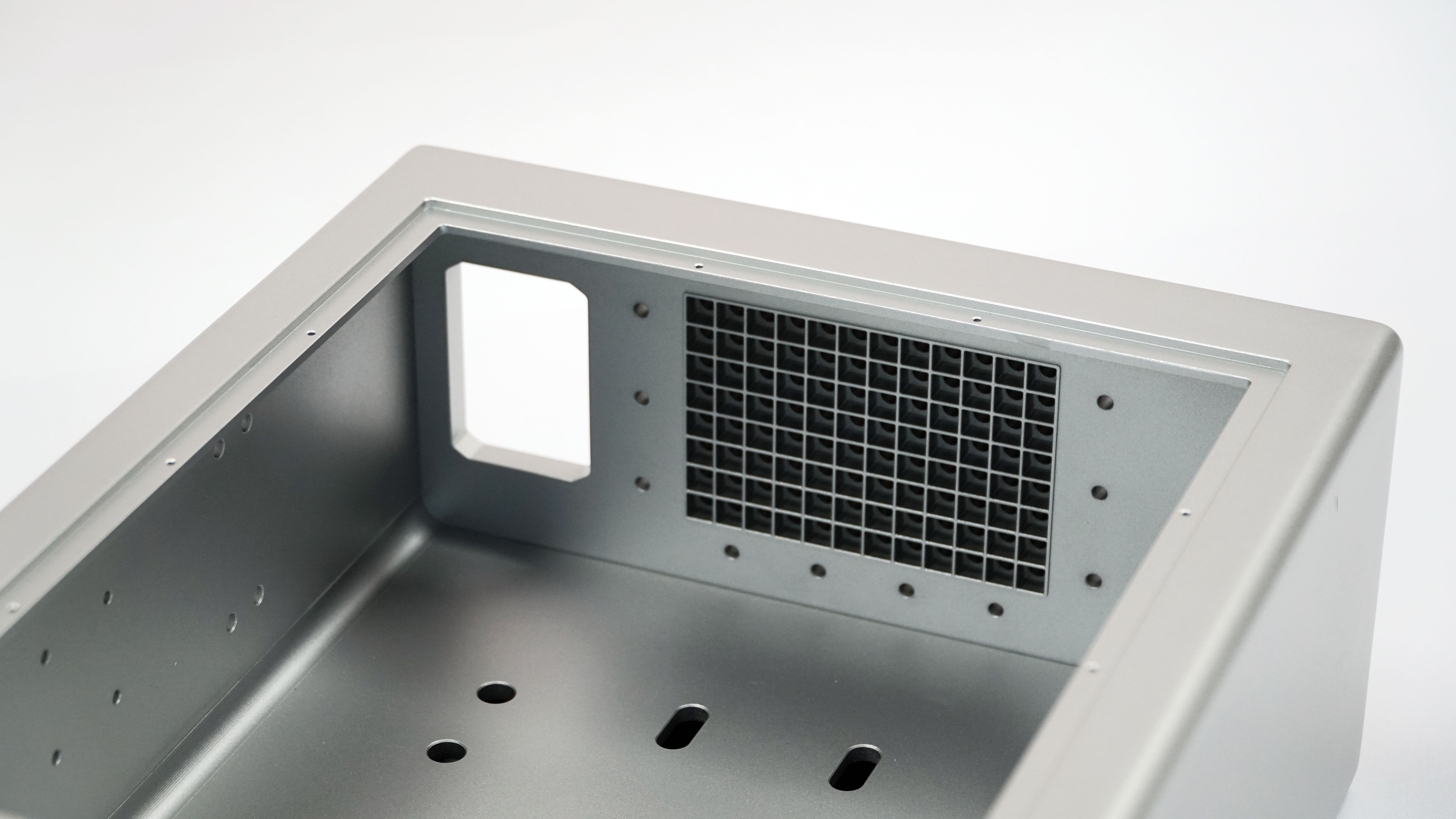
Minimize Tolerance Demands
Tight tolerances require additional machining steps and increase inspection time. Apply high-precision tolerances only to critical functional features. Where less precision is acceptable, use standard tolerances to reduce costs.
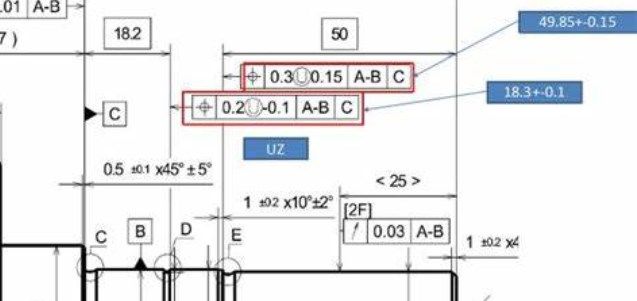
Use Standard Drill Sizes
Non-standard holes or threads may require custom tooling, leading to longer setup times and increased expenses. Always try to design using standardized drill diameters that align with industrial tooling norms.
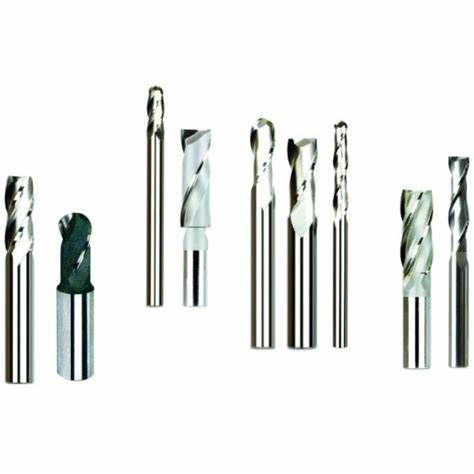
Need CNC Machining?
At Creallo, we offer an AI-powered CNC machining platform designed for B2B customers. Simply upload your 3D CAD files to receive instant DFM feedback, optimized machining suggestions, and a real-time quote—including options for surface finish and lead time.
Let Creallo help you manufacture high-quality parts at reasonable prices—faster and smarter.
