SLS vs MJF: 개발 요구사항에 맞는 최적의 3D 프린팅 방식은?
2025.07.01
SLS? MJF? 어떤 3D프린팅 방식이 더 좋나요?
이 질문은 B2B 제품 개발 현장에서 가장 자주 나오는 질문 중 하나입니다. 하지만 이 질문에는 단 하나의 정답이 존재하지 않습니다. 제조 목적, 제품 크기, 요구 품질, 후가공 옵션, 납기 일정 등 다양한 조건에 따라 적합한 방식은 달라집니다.
이번 콘텐츠에서는 특히 많이 비교되는 두 가지 방식, SLS(Selective Laser Sintering)와 MJF(Multi Jet Fusion) 기술의 특징과 활용 조건을 정리해 드립니다.
기술별 작동 원리 및 특성 비교
SLS (Selective Laser Sintering)
- 작동 방식: CO2 레이저로 나일론 분말을 한 층씩 소결하여 적층
- 주요 소재: PA12, PA11, 알루마이드, 난연/식품 등급 소재 등
- 장점:
- 다양한 소재 호환성
- 대형 부품 출력에 유리
- 높은 강도와 내열성 확보 가능
- 단점:
- 표면이 거칠어 후가공 필요
- 활용 예시: 엔진 하우징, 내열 파트, 기능성 시제품 등
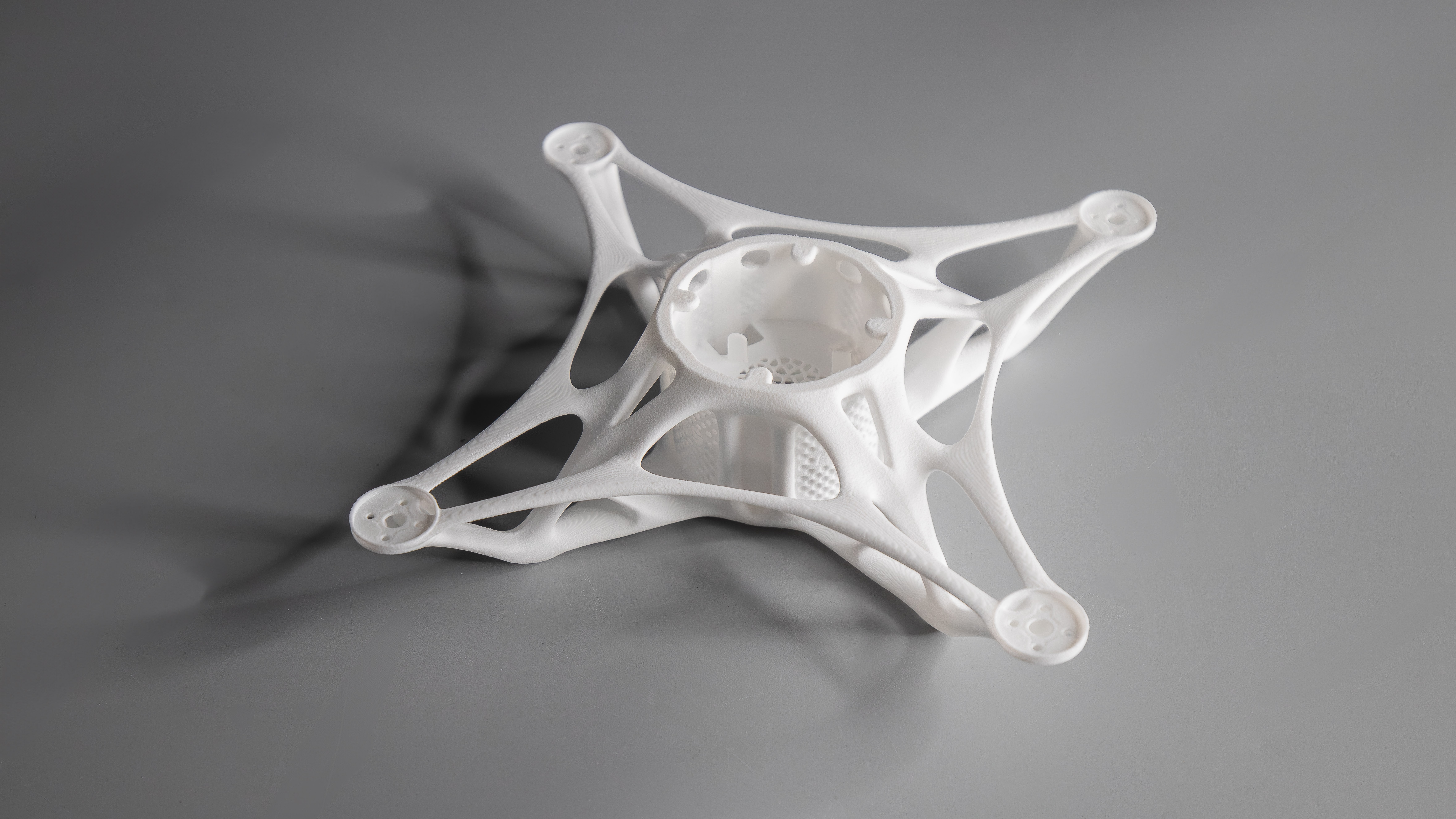
MJF (Multi Jet Fusion)
- 작동 방식: 바인더와 적외선 열원으로 분말을 빠르게 융합
- 주요 소재: PA12, 강화 PA12, PA11, TPU 등
- 장점:
- 고속 출력 가능
- 정밀한 가장자리 구현
- 단점:
- 제한된 소재군
- 출력 색상이 균일하지 않고 회색이 섞여 있음
- 바인더 사용으로 인해 SLS 대비 취성(Brittleness) 있음
- 활용 예시: 정밀 피팅 부품, 기능성 소비재, 양산용 파트
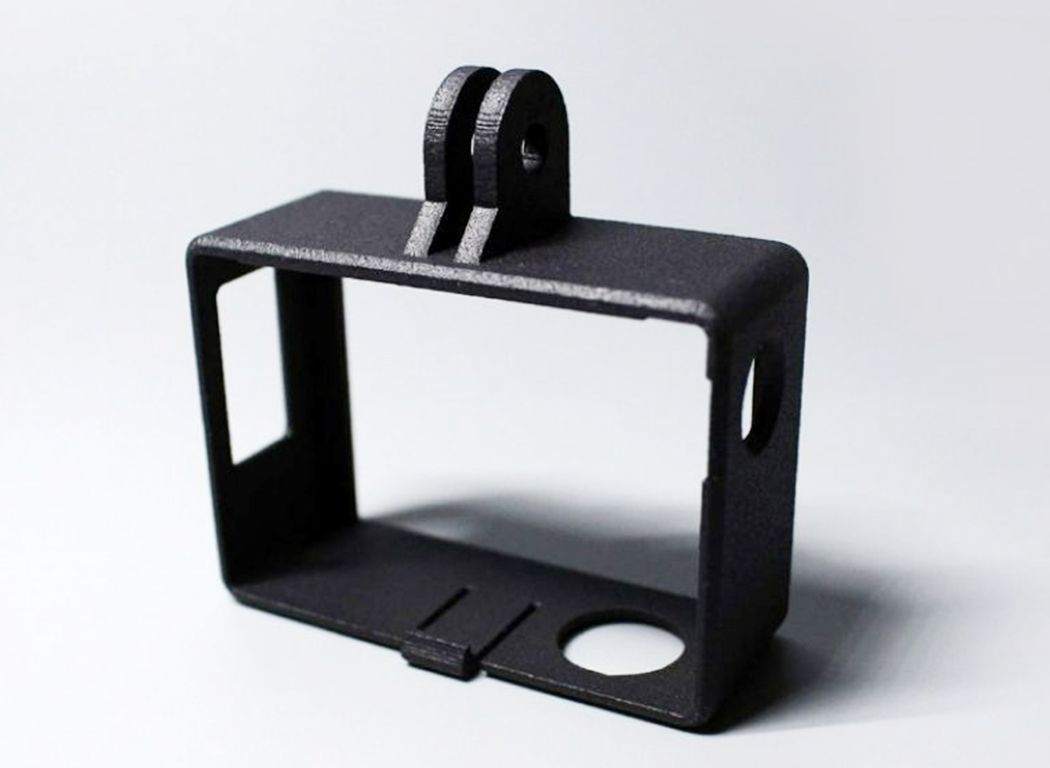
항목별 비교표
항목 | SLS | MJF |
출력 방식 | CO2 레이저 소결 | 바인더 + 적외선 |
기본 색상 | 순백색 | 회색 |
후가공 | 다양한 후처리 가능 | 염색, 도색 제한적 |
소재 호환성 | 다양한 기능성 소재 지원 | HP 전용 소재 중심 |
인체/식품 대응 | 가능 (친환경 소재 활용) | 어려움 (화학 에이전트) |
생산성 | 중형 이상 부품 및 다량 생산 유리 | 소형 부품에 유리 |
유지비용 | 장기 운용 안정적 | 소모품 많고 높음 |
빌드 사이즈
구분 | SLS | MJF |
최대 출력 크기 | 550 x 550 x 750 mm | 380 x 284 x 380 mm |
냉각 시간 | 10~20시간 | 10~20시간 |
MJF와 SLS, 둘 다 활용 가능한 경우는?
두 기술은 때로는 서로 대체하거나 병행 활용될 수 있습니다. 설계 측면에서도 SLS와 MJF간의 공차 차이만 고려한다면 특별히 다른 점은 없습니다.
- 기능 테스트용 시제품
PA11, PA12, 강화 PA12 등으로 강도와 내구성 확보 가능. 브래킷, 하우징, 클립 등에 활용.
- 실사용 엔드유저 파트
연속 생산이 필요한 커넥터, 전자기기 하우징, 소형 기어 등에도 모두 적합.
- 탄성 부품
TPU 소재를 활용한 유연한 씰, 조인트, 가스켓 등 제작 가능.
제조 목적과 조건에 맞는 방식이 가장 중요합니다
SLS가 더 적합한 경우
- 브랜드 색상 표현이 중요한 경우
- 인체 접촉 또는 식품용 부품 제조
- 소량 대량생산을 위한 대형 빌드와 안정성
- 공정 조건 커스터마이징이 필요한 경우
MJF가 더 적합한 경우
- 빠른 납기가 중요한 경우
- 정밀한 디테일과 얇은 벽 두께가 필요한 경우
크렐로에서 바로 출력해보세요
크렐로는 EOS P3 NEXT를 아시아 최초로 도입한 최신 SLS 전문 서비스입니다. 3D 파일 업로드만으로:
- 실시간 DFM 피드백 제공
- 자동 견적 및 납기 확인
- 다양한 후처리 옵션으로 브랜드 품질 유지
를 지원합니다.
단순 부품 출력을 넘어, 고객이 원하는 목적을 더 정확하게, 효율적으로 달성할 수 있도록 지원합니다.
크렐로에서 최신 SLS 3D 프린팅 기술을 경험해 보세요!
