What to Consider When Creating a Medical Device Prototype?
2025.06.18
The Korean medical device industry continues to grow steadily, driven by technological innovation and increased global competitiveness. According to the Ministry of Food and Drug Safety, the market size now exceeds 11 trillion KRW, with an average annual growth rate of 8.3% over the past five years (Source: Medical News). In particular, demand is surging for AI-powered personalized medical devices, digital healthcare solutions, and aesthetic medical technologies.
While functionality was the top priority in the past, the spotlight is now on medical devices that incorporate thoughtful design to enhance diagnostic efficiency and user experience.
The Rise of 3D Printing in Custom Medical Devices
3D printing is increasingly used to create patient-specific medical devices. By enabling complex anatomical structures that are difficult to reproduce with traditional methods, 3D printing improves both usability and functionality. These technologies are widely applied across orthopedics, reconstructive surgery, prosthetics, implants, dental applications, and even veterinary medicine.
With this shift, medical device prototyping has become a vital step in the development process. A prototype allows for performance testing, early detection of design flaws, and refinement before mass production. It helps reduce lead time and production costs and is essential for meeting global certification standards, especially for international market entry.
So, what should companies keep in mind when prototyping medical devices? Let’s explore.
1. Choosing the Right Materials and Processes
Selecting the optimal manufacturing process and materials is critical to ensuring that the prototype reflects the intended design and performance. Below are three commonly used methods in medical device prototyping:
3D Printing | CNC Machining | Vacuum Casting | |
Key features |
|
|
|
Suitable Materials |
|
|
|
Common Applications |
|
|
|
To ensure optimal results, consult manufacturing experts to determine the right process and material combination based on functionality, budget, and production scale.
When choosing materials for devices that come into direct or indirect contact with the human body, the following must be verified:
- Biocompatibility: The material must not trigger toxicity or allergic reactions.
- Durability & Mechanical Properties: It should provide suitable strength and flexibility.
- Sterilizability: The material must withstand sterilization without deformation.
Thorough consideration of these factors ensures safety and performance in the final product.

2. Design Optimization
Design is a foundational element in developing safe and functional medical devices. During the early stages, it’s essential to understand the limits of each manufacturing process to minimize design errors and reduce production costs.
- 3D Printing: Can handle large and intricate designs if sufficient wall thickness is maintained.
- CNC & Vacuum Casting: More limited in design flexibility. Undercuts, for example, require special attention.
Each process also comes with different tolerances that affect part assembly. It’s important to account for this during the design phase.
Creallo provides design guides tailored to these constraints and helps optimize prototypes from the beginning.
AI-Powered Design Feedback
Creallo’s AI-driven online manufacturing platform analyzes your 3D design files in real time. By automatically detecting problematic features and suggesting adjustments, it significantly shortens design cycles and prevents costly mistakes.


3. Regulatory Compliance & Certification
To enter domestic or global markets, medical devices must meet strict regulatory and safety standards. Below is a comparison of the major certifications:
주요 인증 비교
Certification | KGMP | ISO 13485 | FDA | CE |
Description |
|
|
|
|
Region |
|
|
|
|
Key notes |
|
|
|
|
Distinct Features |
|
|
|
|
When developing a prototype, understanding the target market’s regulatory framework is essential. Creallo supports compliance by adhering to international standards, including ISO 9001:2015, ensuring reliability and quality in every stage of production.
4. Testing and Iteration
Medical device prototypes should be tested in simulated real-world environments, with feedback from users and healthcare professionals driving continuous improvement. This iterative process is key to eliminating design flaws and ensuring readiness for commercial release.
Close collaboration with a responsive manufacturing partner is crucial for fast iteration. It’s also important to allocate sufficient time for testing from the earliest stages of development.
Final thoughts
At KIMES 2025, Korea’s premier medical device exhibition, Creallo’s vacuum-cast menstrual cup—made from TPU-like PU—drew significant interest from visitors. This material allows developers to evaluate hardness and user comfort without the high cost of silicone molding, highlighting Creallo’s deep expertise in material selection and rapid prototyping.

From concept to creation, Creallo assigns dedicated project managers to help medical device companies turn ideas into functional, high-quality prototypes. With proven expertise in 3D printing, CNC machining, and vacuum casting, Creallo delivers cost-effective, production-ready solutions tailored to your needs.
Prototyping is the first crucial step toward a successful product launch. Though the process may seem complex, Creallo offers the guidance, tools, and manufacturing know-how to help you succeed.
Start your medical device prototyping journey with Creallo—faster, smarter, and more reliable.
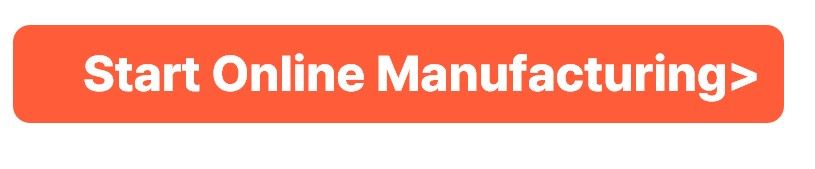
Related links: